Poiché i due regolatori della cella di Peltier dovranno gestire una corrente di circa 3A, è opportuno dissiparne il calore. Seguendo i suggerimenti di Paolo (ariadivetro.it) ho portato all’esterno i due componenti, di modo da poterli raffreddare più agevolmente.
Avendo la possibilità di accedere a molto materiale informatico in disuso, ho recuperato un po’ di dissipatori in alluminio, ma mentre cercavo una buona soluzione per il problema, mi sono accorto che il TIP2955 e il 78T12 hanno la terra collegata con la lnguetta di fissaggio: controllando lo schema, ho notato che la il collettore del TIP viene collegato con l’uscita del 78T12, ma le due masse non devono essere collegate. Per questo motivo ho ritenuto opportuno utilizzare due dissipatori isolati l’uno dell’altro.
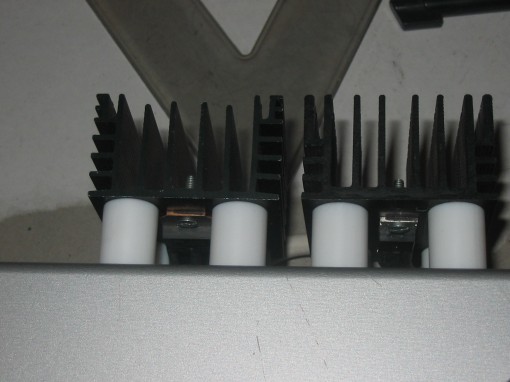
Dissipatori per TIP2955 e 78T12
I due dissipatori sono sostenuti da blocchetti in teflon, i quali sono, a loro volta, fissati tramiti viti parker: i blocchetti sono lunghi 17mm, per evitare che le viti parker venissero a contatto al loro interno, vanificando il proposito di isolamento. Il TIP e il 28T12 sono fissati ai dissipatori tramite brugolette da 3; prima di bloccarli ho provveduto a applicare delle pasta conduttrice sul retro.
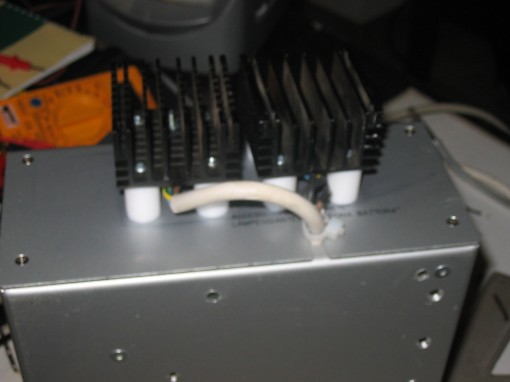
Alimentatore, cavi verso i dissipatori
Visto che questi componenti saranno soggetti alle intemperie esterne, ho ricoperto tutti i piedini con della guaina termorestringente, inoltre i due cavi sono bloccati, sia all’interno che all’esterno, da due fascette di plastica, per evitare che possano sfilarsi accidentalmente.
Simone